Design of an Underwater Towfish Using Design by Rule and Design by Analysis
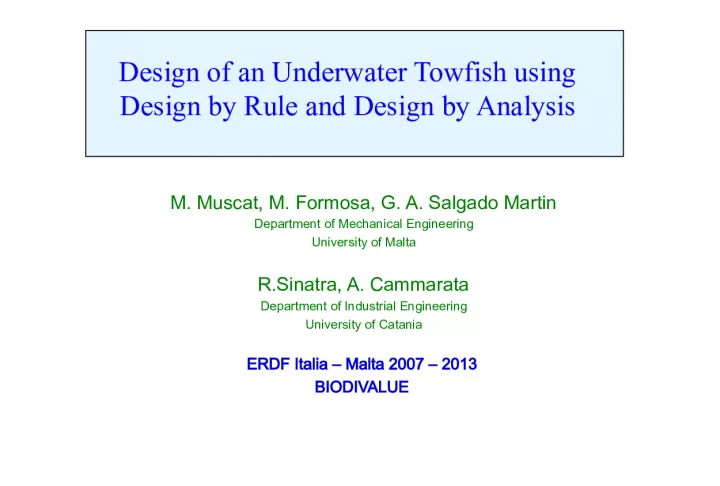
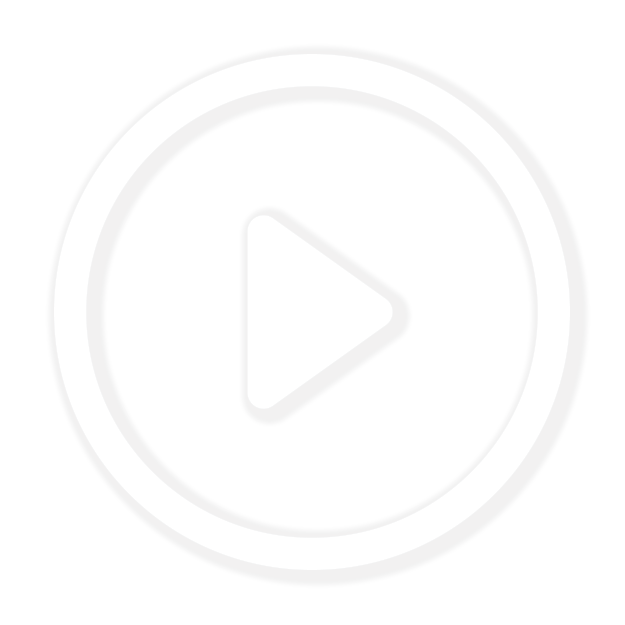
This project presents the scope and methodology of designing an underwater towfish using design by rule and design by analysis. The project includes the description of the towfish, its design process, and the prototype manufacturing.
- Uploaded on | 0 Views
-
marlottedoomen
About Design of an Underwater Towfish Using Design by Rule and Design by Analysis
PowerPoint presentation about 'Design of an Underwater Towfish Using Design by Rule and Design by Analysis'. This presentation describes the topic on This project presents the scope and methodology of designing an underwater towfish using design by rule and design by analysis. The project includes the description of the towfish, its design process, and the prototype manufacturing.. The key topics included in this slideshow are Underwater Towfish, Design by Rule, Design by Analysis, Prototype Manufacturing, Methodology,. Download this presentation absolutely free.
Presentation Transcript
1. Design of an Underwater Towfish using Design by Rule and Design by Analysis M. Muscat, M. Formosa, G. A. Salgado Martin Department of Mechanical Engineering University of Malta R.Sinatra, A. Cammarata Department of Industrial Engineering University of Catania ERDF Italia Malta 2007 2013 BIODIVALUE
2. SUMMARY OF PRESENTATION Scope for the project Description of the towfish Methodology of Design Design by Rule Design by Analysis Conclusions and Discussion Prototype manufacturing
3. Scope for the project Monitoring of sea water pollution Monitor jellyfish population Monitor plankton population The towfish is very convenient to use when a large area of the sea needs to be scanned
4. Description of the Towfish An underwater vessel towed behind a surface ship The towfish is equipped with various sensors & cameras Positively buoyant Depth of dive controlled by hydroplanes Maximum depth of dive is 50m Data, signals, power transferred via tow line
5. Description of the Towfish
6. Methodology of Design The Design of the Towfish is not governed by international legislation or code of standard The towfish can be considered to be a pressure vessel acted upon by external pressure and various local loads DBR first used to calculate some of the various dimensions and thicknesses of the towfish components mainly to prevent buckling DBA Annex B of EN13445 part 3 was then used to carry out other buckling checks that were not possible with DBR
7. Design by Rule Section 8 & Section 16 of EN13445 Part 3 Main cylindrical, hemispherical, conical shell & cylindrical arms designed against buckling (Section 8) Section 16 used to check for any reinforcement required due to local loads acting at the nozzle attachments and at the towlug area
8. Design by Rule Methods presented in EN13445 not always applicable for the design of the towfish components. Conical end bearing reinforcement Rectangular flange connection of the fixed part of the hydroplane to the main cylinder
9. Design by Rule
10. Material used for the towfish Structural steel Minimum yield stress R eH of 235 N/mm 2 Maximum tensile stress R m of 360 N/mm 2 Resulted in a Design stress of f of 150 N/mm 2 Corrosion allowance not required
11. Design by Rule (Buckling) The internal flanges connecting the main cylinder to the hemispherical and to the conical ends were assumed to act as heavy stiffeners No need to include shell junction reinforcements Buckling expected to occur within each main shell component
12. Design by Rule (Buckling) Main cylinder thickness 3mm Cylindrical arms thickness 2mm Hemisphere thickness 2mm Conical end thickness 2mm
13. Design by Rule (Local loads) Total lift on both hydroplanes was -702N Total drag on the towfish was 2519N Lift on each rotating aileron was -254N Drag on each rotating aileron was -87N Lift on each fixed part of the hydroplane was -97N Drag on each fixed part of the hydroplane was 100.6N
14. Design by Rule (Aileron nozzle) As a conservative assumption, for the DBR part it was assumed that each aileron nozzle on the main cylinder side is carrying the lift and drag acting on each aileron DBR section 16 of MSA EN 13445-3 resulted in a reinforcement plate of thickness 3mm for the region of the aileron nozzle The reinforcement was also extended so that it reinforces the area around the rectangular flange connection of the fixed part of the hydroplane
15. Design by Rule (Towlug) By considering the lift and drag on the hydroplanes and towfish, the maximum value and direction of the resulting force on the towing lug could be calculated This resulted in a reinforcement plate of 3mm thickness in the towing lug region.
16. Design by Rule (Towlug)
17. DBR (conical end nozzles) For the design of the nozzles at the conical end the assumption that the local loads are acting on a cylinder having the same diameter of the cone at the point of the nozzle/bearing connection was taken. No reinforcement required
18. Design by Analysis ANSYS Mechanical used within a DBA context in order to ascertain the structural integrity of the towfish especially in the parts that deviated away from the scope of Sections 8 and 16 of EN13445-3 GPD & I design checks were carried out to ensure structural integrity of the pressure vessel component
19. Finite element models Partial safety factors for the material different for GPD & I checks For the GPD check the yield stress value used in the finite element material model was 162.8 N/mm 2 For the I check the yield stress value was 235 N/mm 2 .
20. For the buckling check of the towfish no pre- deformations according to the critical eigenvalue buckling shapes were considered. Local loads acted as force or moment perturbations to induce buckling Partial safety factors for pressure action and local load actions applied Linear elastic perfectly plastic material model The finite elements SHELL281 and BEAM181 were used in the software ANSYS Mechanical
21. For all the FEA models (except for the towlug model) the nozzle moments created a situation of geometrical weakening so that both GPD and I check used large deformation analysis. For the towlug model only the I check required the use of large deformation analysis.
22. GPD / I check on aileron nozzle/main cylinder Same loading situation as in the DBR method Pressure acting on the cylindrical shell & hydrodynamic lift and drag acting on the aileron Fully fixed BC at the flanges Symmetry BC along length of cylinder
23. The reinforcing plate in the region of the nozzle as described in the DBR section of this paper had a thickness of 3mm so that the total shell thickness in this region was 6mm. The cylindrical shell thickness elsewhere in the model was 3mm. The model deformation was as expected and confirmed the applied boundary conditions and loadings.
24. GPD / I check on aileron nozzle/main cylinder The figure shows the von Mises stress obtained from the I check on the top surface of the shells. Yield stress 235N/mm 2 In the region of the nozzle the material remains wholly elastic with principal structural strains much below 5%
25. GPD / I check on aileron nozzle/main cylinder The lift and drag on the ailerons is counteracted by both aileron nozzles that is the one on the main cylinder side and the one on the cylindrical arm side. Different from what was designed using DBR but is more faithful to the towfish prototype design
26. GPD / I check on aileron nozzle/main cylinder The model includes the loading at the end of the fixed wings due to the hydrodynamic drag and buoyancy of the cylindrical arms. The model deformation was as expected and confirmed the applied boundary conditions and loadings.
27. GPD / I check on aileron nozzle/main cylinder von Mises stress obtained from the I check on the top surface of the shells. In the region of the aileron nozzleand fixed wing connections the material remains wholly elastic with principal structural strain much lower than 5%.
28. GPD / I check on elevator nozzle/conical end FE model used for the check against buckling for the region of the elevator nozzle connection to the conical end. The conical shell has a thickness of 2mm while the thickness of the shell for the nozzle is 5mm.
29. The model deformation was as expected and confirmed the applied boundary conditions and loadings. The maximum principal structural strain occurred in the elevator nozzle/conical shell region and had values of 0.667% in the GPD check and 0.293% in the I check.
30. GPD / I check on the towlug/main cylinder The thickness of the towlug shell is 4 mm. The thickness of the reinforcing plate region is 6mm. The cylindrical shell thickness elsewhere in the model is 3mm. The reinforcing plate in the region of the towing lug is of rectangular shape and has dimensions 70mm by 200mm.
31. GPD / I check on the towlug/main cylinder In the region of the towlug area the material remains wholly elastic with some plasticity occurring in the internal flange that connects the main cylinder to the hemisphere. The maximum structural strain for both the GPD check and the I check occurred in the flange regions and was much less than 5%.
32. Discussions and Conclusions The DBR approach and assumptions taken were quite suited for the preliminary design of the towfish. DBA is required in order to get more insight into the kind of failure mechanisms especially for the components that were outside the scope of the DBR method. At the main cylinder internal flanges some plasticity has occurred. In case that this plasticity may effect the service conditions of the flanges and so their thickness was increased to reduce the size of the plastic region.
33. Discussions and Conclusions In all components the maximum structural strain in the FEA models when subjected to the maximum loads was less than 5%. Therefore the principles of the GPD check and I check were satisfied and the design of each component acceptable according to Annex B of EN13445 Part 3 DBA can be further used to reduce the weight of the towfish while at the same time maintaining its structural integrity and fitness for purpose as regards to allowable deformations.
34. Prototype Manufacturing Main changes to the original design : Flange tickness equal to 5 mm for all collars. Thickness reduced from 2 mm to 1,5 mm for ailerons, stabilizers and rudder. Cutting of the central screw to allow screwing of the main body to the ailerons. Skid supports moved to the central bodys external surface. Modified flange system for the camera housing (pods cap) conical surface approximated through planar surfaces
35. Assembly of the Prototype Front view assembly of the prototype
36. Rear view assembly of the prototype Assembly of the Prototype
37. Coupling Flange Flange used for the coupling of the rudder motor to the shaft. Connection flange-shaft is made using hole with steel plug
38. Rudder Motor View mouting of the motor and rudders shaft.
39. Motor Support Motor support and anchorages to the towfish frame Holes: 2 dof
40. Cone Assembly Inside view of the cone assembly. Particular view assembly of the stabilizers and rudder
41. Fixed Wing Support view of the fixed wing support The component has been modified to remove the problems associated with the screwing
42. Cone support removible part while operating Supports fixed on the towfish cylinder by welding
43. Ailerons
44. Ailerons motor support Welding View inside the main body
45. Open Pod Pod without cover to position a GoPro Camera
46. Close Pod Pod with cover
47. O-Ring Stabilizers O-Ring housing
48. Thank you for attending