Wayne L Morse Federal Courthouse in Eugene, OR
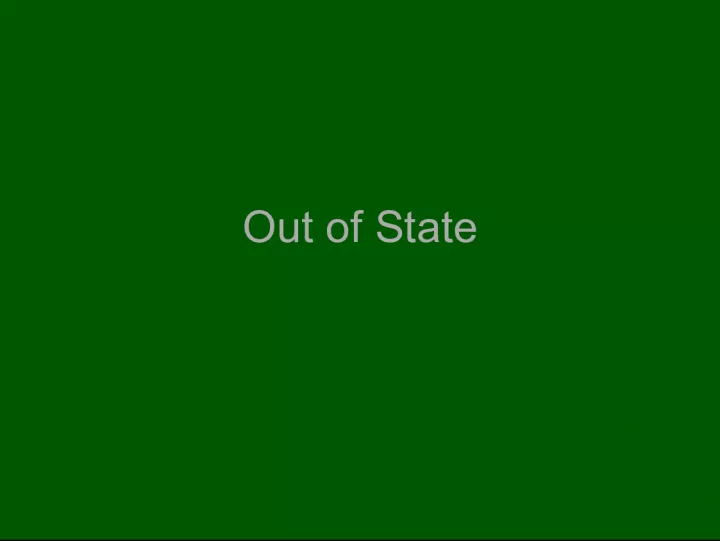
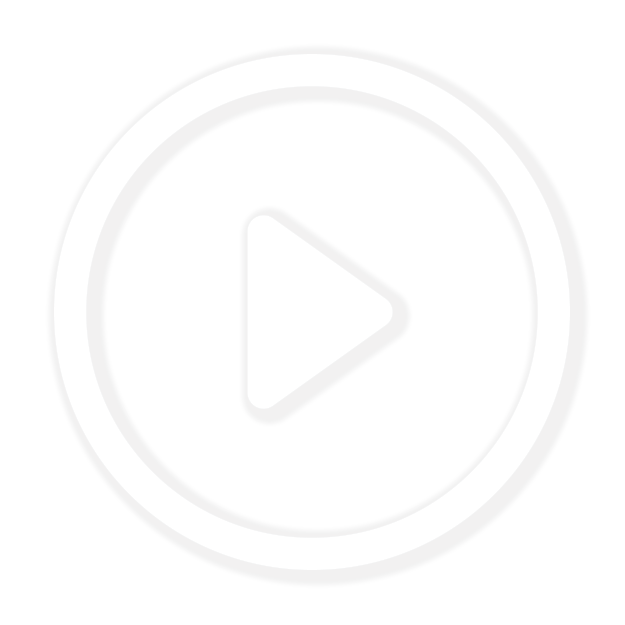
The Wayne L Morse Federal Courthouse is a high-performance building located in a mid-size city setting in Eugene, OR. Managed by the U.S. General Services Administration, it is a state-of-the-art facility that promotes energy efficiency and sustainability.
- Uploaded on | 0 Views
-
anniwirta
About Wayne L Morse Federal Courthouse in Eugene, OR
PowerPoint presentation about 'Wayne L Morse Federal Courthouse in Eugene, OR'. This presentation describes the topic on The Wayne L Morse Federal Courthouse is a high-performance building located in a mid-size city setting in Eugene, OR. Managed by the U.S. General Services Administration, it is a state-of-the-art facility that promotes energy efficiency and sustainability.. The key topics included in this slideshow are Wayne L Morse Federal Courthouse, Eugene OR, mid-size city setting, U.S. General Services Administration, high performance building,. Download this presentation absolutely free.
Presentation Transcript
1. Out of State
2. Wayne L. Morse Federal Courthouse Eugene, OR / Mid-size city setting U.S. General Services Administration High Performance Characteristics Sustainable Site Building orientation and primary entrance are located to promote pedestrian access and encourage the use of mass transit systems Extensive landscaping minimizes storm water runoff from impermeable surfaces Water Efficiency Low flow toilets and faucets with infrared on-off valves conserve water Energy and Atmosphere High-performance motors reduce drive and winding losses in the mechanical equipment Entire building perimeter is clad in glazing to maximize natural light Lighting design meets Energy Star requirements Underfloor air, radiant slab heating and cooling Operable windows at the chambers level feature heating and cooling systems that are de- activated by an open window Occupancy sensors control lighting in unoccupied spaces Materials and Resources Smaller building minimizes quantity of building materials Durable materials minimize life cycle cost repairs Certified sustainably managed wood products Indoor Environmental Quality Selected materials maximize indoor air quality Glazing and fixture selections balance daylighting and artificial lighting to provide glare- free, low-contrast light Mechanical system and chambers-level operable windows enable continuous ventilation Displacement ventilation air delivery system minimizes noise Air intake vents are located away from sources of pollution and exhaust air Exposed concrete flooring and cleanable surfaces reduce dust and allergens Mechanical systems and ducts were isolated or sealed off during construction to avoid contamination LEED RATING LEED Gold Certified PROJECT TEAM: DLR Group in Association with Morphosis is the Architect of Record, and provided Engineering and Construction Administration Services. Commission on the Environment Architecture Engineering Planning Interiors Awards/Publications LEED Gold Certified National Center for State Courts/Retrospective of Courthouse Design Selection, 1991-2001 U.S. General Services Administration, Design Excellence Competition, 1999 U.S. General Services Administration Design Award Citation in the On the Boards category, 2002 Architecture magazine 2004 Progressive Architecture design award Architectural Record: Looking to Redefine its Designs, Sept. 1999 Northwest Construction: DLR Group Honored by GSA for Courthouse Design, July 2004 Architecture Magazine: Eugene Courthouse Design Recognized, March 2004
3. Chino Valley Agribusiness + Science Technology Center Chino Valley, Arizona Yavapai College District PROJECT TEAM: DLR Group Commission on the Environment High Performance Characteristics Sustainable Site Native vegetation restored areas disturbed by construction Required over-excavation and masonry debris were retained on site and integrated into the landscape design Water Efficiency Harvested rainwater and Xeriscape landscaping reduce water use Storm water runoff collects in engineered wetlands Water from engineered wetlands provides irrigation for the golf course Energy and Atmosphere 2.4kW photovoltaic array Natural daylight harvesting used throughout building Continuous dimming ballasts controls with indirect fixtures Deep overhangs protect windows from harsh high desert sun and reduce solar heat gain Solar hot water heating reduces energy consumption Geothermal heat pump system Operable windows Comprehensive energy management control system The building reduces energy use by more than 50% below ASHRAE 90.1- 1999 standards Roof cupolas provide natural ventilation Materials and Resources Regionally/locally produced materials reduced energy use in transportation: Nearly 50% of the materials in the project were manufactured within a 200-mile radius of the site A majority of the wood used in the project is certified by the Forestry Stewardship Council All adhesives, paint and interior products are low-emitting materials Locally manufactured post-tensioned masonry provides a durable interior and exterior finish, as well as thermal mass and insulation Project achieved a 50% construction waste-recycling goal Awards/Publications AIA Arizona: 2003 Client of the Year Award AIA Arizona: 2005 Energy Award Arizona Public Service: 2005 APS Energy Award Southwest Contractor magazine: Best of 2004 Green Building Under $5 million School Construction News, May/June 2005: Rural College Boasts LEED Silver Certification LEED RATING LEED NC Silver Certified - 2005 Architecture Engineering Planning Interiors
4. 6225 North 24 th Street Tenant Improvement Phoenix, Arizona High Performance Characteristics Sustainable Site Site is located on two major bus lines On-site showers and bicycle storage support alternative transportation for employees Car pools receive priority parking On-site shade provides heat mitigation for parking Water Efficiency Low-Flush toilets Low-flow aerators on all faucets Low-water use landscaping with drip irrigation Energy and Atmosphere Carbon dioxide sensors ensure that the appropriate amount of fresh air is brought into the building Networked printers and EnergyStar equipment operate well below standard office energy needs Materials and Resources Low VOC paints Green Seals GS-11 requirements Regionally/locally produced materials reduce energy use in transportation Carpet produced by solar-powered mill Sustainably produced materials and materials with recycled or rapidly renewable content Extensive reuse of existing building components (doors and frames, ceilings, glass partitions, casework) reduced construction waste 100% of the floor, 85% of original ceiling and 25% of the existing walls were retained in construction Indoor Environmental Quality 90% of regularly occupied spaces feature direct lines of sight to perimeter glazing Green cleaning program uses environmentally friendly maintenance products Employees participate in recycling program for paper, corrugated cardboard, glass, plastics and metals LEED RATING LEED CI Certified 2004 (First in Arizona) PROJECT TEAM: DLR Group Commission on the Environment Architecture Engineering Planning Interiors Awards/Publications LEED CL 2004 Location: Phoenix, AZ / Urban Setting Building type: Office building Occupancy type: Typically occupied 50 hours per week approximately 52 weeks per year The 6225 North 24 th Street office project is an renovation of a 30,000-SF portion of a 1984 office building. The design goal was to model an environmentally intelligent, office renovation and to create a healthy, pleasant environment for its employees
5. Penn State University Medlar Field at Lubrano Stadium State College, Pennsylvania High Performance Characteristics Sustainable Site Re-use rock dug out of the outfield as fill material to level the playing field Site was not environmentally sensitive Parking shared with the existing Bryce Jordan Center Trees added in parking areas to reduce the heat island effect Alternative / mass-transit options encouraged Water Efficiency Use of waterless urinals and low-emitting materials Faucets, with auto-control, have low flow of 0.5 gallons/minute. Shower head in the locker rooms provide 1.5 gallons of water per minute. Energy and Atmosphere Power provided in part by a wind turbine system Occupancy sensors are located in private areas (offices) Additional, third-party commissioning reviewed the facilitys proper usage of the HVAC, lighting, electrical, and plumbing systems Materials and Resources Stadium is connected to an existing gray water system that also serves nearby Beaver Stadium 75 percent of the construction waste was diverted to areas other than landfills The stadiums CMU block was manufactured by a local contractor Indoor Environmental Quality Plenty of daylight is allowed into the offices, box areas, concourse, and seats to reduce the amount of lighting energy needed during the day. Over 15% of the materials used were made from recycled content and 40% of the materials were manufactured regionally, including the concrete shown in the photo. LEED RATING LEED NC Silver Certified Only LEED Stadium PROJECT TEAM: L. Robert Kimball (architecture) DLR Group (architecture) Commission on the Environment Architecture Engineering Planning Interiors Awards/Publications LEED Certified American School & University Architectural Portfolio: Specialized Facility Citation MidAtlantic Construction magazine Best of 2006 Sports Category Learning by Design 2007 Mid-Atlantic Construction, 2006: Best of Sports Award Ballpark Digest, May 2005: Penn State approves new ballpark Building Design & Construction, Sept. 2007: Penn State wins race for first LEED-certified stadium Opening Press: Penn State University, July 2005: Centre Daily Times, Jan. 2006: Medlar Field on Schedule for May 31, 2006 Completion Date Daily Collegian, May 2006: New Stadium Awaits Grand
6. Washington State Penitentiary Warehouse Replacement Walla Walla, Washington Washington Department of Corrections High Performance Characteristics Sustainable Site High albedo concrete and roof color mitigate heat islands and reduce cooling costs Commuter bike racks and showers Full cut-off site lighting reduces light pollution. Water Efficiency Waterless urinals Non-potable water collected for irrigation Energy and Atmosphere Significant day lighting North-facing skylights provide low temperature indirect lighting Ground-source heat pump with geothermal coils heats and cools the building No mechanical cooling in high bay spaces Heat exchangers pump heat from warehouse freezers and other building systems into domestic and hydronic water heating system Nighttime purge of warm indoor air lowers building mass temperature for daytime cooling. Materials and Resources Certified wood products Construction waste recycling Indoor Environmental Quality No smoking with in 25 feet of any entrances or ventilation intake areas Low-VOC-emitting materials: Adhesives, paint, carpet and composite wood products LEED RATING LEED NC Silver Certified - 2005 PROJECT TEAM: DLR Group Commission on the Environment Architecture Engineering Planning Interiors Awards/Publications LEED NC Silver Certified ASHRAE - Puget Sound Chapter Technology Award for 2007, New Industrial Facilities or Processes Judges: This project exemplifies the innovative use of new technologies to meet the demands of IAQ, energy efficiency, operations and maintenance, cost effectiveness and environmental impact. Correctional News: March/April 2006: Washington State Green Warehouse Could Reduce Operations Costs IRMA: November 2005: Prison Warehouse Earns a LEED Silver Certification